DI and DRD Tin Cans
Shallow drawn cans
Shallow containers, made by a single draw from a flat sheet of tinplate, may be finished cans for products like sardines or pies or they may be the first step in the manufacture of two-piece deep drawn containers which are described next. Shallow drawn cans may be round or square in cross-section and, with the application of special forming techniques may be produced with tapered walls in a single draw. Tapered walls permit the empty cans to be nested for more economical shipment over long distances. Single draw cans for food or general line purposes provide an ideal application for the use of distortion printed tinplate.
Drawn and wall-ironed cans
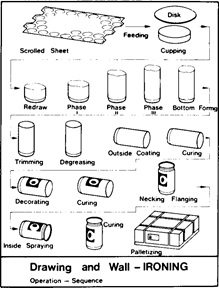
The development of the draw and wall ironed (D&I) can began in Switzerland during the Second World war
when tinplate became virtually unobtainable for package manufacturing and aluminium was the only other material available. As aluminium could not be used for making three-piece cans, it was necessary to develop a seamless form of can body instead. Some twenty years later, in 1963, the first commercial aluminium D&I beer cans were made and filled in the USA. Only when the steel substrate could be made clean enough could the D&I process be adapted to use tinplate. The major application for the D&I can is for beer and beverage cans, although the use of tinplate D&I cans for both human and pet foods is now well established in both the USA and the UK.
D&I cans are most appropriate where large volumes of cans with similar specifications are required. In these situations, where cans with a large height to diameter ratio are required, the D&I process is the most economical of all the known can manufacturing processes in terms of metal utilisation.
- Figure - Flow line for the manufacture of a drawn and ironed two-piece tinplate can volumes of cans with similar
Plain tinplate, in coils of approximately 10 tonnes weight and up to 1200 mm in width, is the starting material for D &I can manufacture The tin coating is normally left in the unflow melted state to maximise the amount of free tin available to act as a lubricant during the wall ironing process. Prior to the first forming operation a water based drawing lubricant is applied to both sides of the metal. Using a double action cupping press, multiple discs are blanked-out across the full width of the coil and then, in the same tooling stations, drawn into shallow cans, dimensions
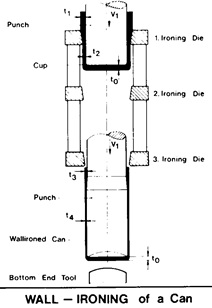
Schematic view of the wall ironing process at this stage are typically 82mm in two-piece D & I can manufacture) diameter and 34mm height. The cups then enter the wall ironing bodymaker. Modern commercial units are single action horizontal power presses, with redraw facility, capable of operating at 300 – 500 strokes/min. depending on can type and size. A special punch, which has the same external diameter as the inside of the finished can, forces the cup through a series of annular dies (Figure above), the first of which redraws the cup to the finished can diameter; the remaining dies iron the wall of the can, reducing its thickness and at the same time increasing the overall body length. The base remains constant in thickness and diameter during the ironing process. At the end of the forward stroke, after the can has passed through all the wall ironing dies, its base is domed to give it greater strength.
The ironing results in a very bright finish on the formed body. The can is removed from the punch, after forming, by a stripping mechanism. It then passes to a trimmer which removes the irregular top edge and leaves a can shell with the precise wall height required for later forming operations. Trimmed cans travel to a washing unit where they are chemically cleaned, to prepare the surface for receiving exterior and interior organic coatings. Because of the extreme deformation which the metal had to undergo during the drawing and ironing process, it was necessary to virtually submerge the can in a continuously circulating lubricant / coolant. All traces must therefore now be removed during the washing operation. Proprietary chemical cleaners are used for this purpose followed by rinses in fresh and finally de-ionised water.
The next stages are coating and decorating. Unlike three-piece cans, the metal cannot be decorated in the flat and special coating and printing units are employed to operate on the external surface of the cylindrical body. Whilst the decoration is still wet, a coat of varnish is also applied to the bottom rim and part of the concave dome of the base. The whole is then cured. Protective lacquer is sprayed inside the cans followed by baking to remove all the solvent and cure the coating. Two interior coatings may be applied, with curing after each application, especially when soft drinks are to be packed. For drinks cans, the final operations involve a reduction in diameter of the top of the can (neckingin), followed by outward spin flanging to prepare the can for closure. Neckingin allows the end seam to be kept within the diameter of the can body for ease of stacking. It also allows a smaller diameter can end to be used, providing material savings. For processed food packaging, the D&I can is not necked-in but has a flange formed by spinning. The walls are then beaded for additional strength, to prevent implosion of the can during the thermal sterilisation process. Finally, all cans are tested to ensure freedom from leaks.
This D&I can-making process imposes severe requirements on the quality of the steel substrate. It must be clean to avoid an unacceptable level of wall splits or flange cracks; composition must be controlled to give correct temper and formability; drawability and earring can influence operational performance, e.g. stripping from punches; the number of pinholes and welds must be controlled; gauge control within strict tolerances is essential.
Draw-redraw cans
Seamless two-piece cans are also produced by a sequential drawing operation known as draw-redraw (DRD). In this process, the can walls are not thinned and therefore containers may have sufficient strength to withstand processing without body beading.These cans are suitable for holding foodstuffs such as tuna fish, salmon, some fruits, vegetables and meats. However, the walls of DRD cans are thicker than is strictly needed which is wasteful in material. Sizes are best restricted to those with small height to diameter ratios where the material contained in the can wall represents a lesser proportion of the total. The process has considerably lower installation costs than drawing and ironing and is generally best suited to smaller annual production volumes e.g. 50-200 million per annum. Line speeds for DRD are normally in the range of 50-1000 cans per minute.
In the draw-redraw process, can bodies are produced in two or more stages from flat pre-coated tinplate. The number of drawing stages depends on the height to diameter ratio of the container required. The material used for DRD cans is usually pre-coated with lacquer or polymer film on both sides in either coil or sheet form.
The material is fed into the first stage, which cuts a circular blank and draws a shallow cup in one operation. The press used for this operation is similar to that used for cupping in the D&I process.These cups are then transferred to a second press for redrawing. Normally this press will also form the base panel in the can. The last drawing operation is usually not completed, leaving a flange of uneven width. The flange is then die trimmed to leave a clean edge of consistent width for seaming.
Cans may be beaded to give the walls extra rigidity. The bottom portion of the can wall may be stepped-in to permit easy stacking. Tapered cans have also been developed, principally for salmon products, which are fully nestable to reduce shipping costs. Irregular (oval and rectangular) DRD cans are also produced by the same basic process for various fish and meat products.
- Source: The International Tin Association (formerly ITRI Ltd)