Investment Casting
- Investment casting is also known as the lost wax process. This process is one of the oldest manufacturing processes. Very fine surface finishes and excellent reproduction of detail are some characteristics of investment casting. Inricate shapes can be made with high accuracy. In addition, metals that are hard to machine or fabricate are good candidates for this process.The process first requires the manufacture of an intricate metal die with a cavity in the shape of the finished product. Special wax, plastic or a low melting alloy is cast into the die, the removed and carefully finished with heated tools.
- This wax pattern is dipped in refractory slurry, which coats the wax pattern and forms a skin. This is dried and the process of dipping in the slurry and drying is repeated until a robust thickness is achieved. After this, the entire pattern is placed in an oven and the wax is melted away. This leads to a mold that can be filled with the molten metal. Metal is introduced into the mold cavity and allowed to cool at a controlled rate.
- The materials used for the slurry are a mixture of plaster of Paris, a binder and powdered silica, a refractory, for low temperature melts. For higher temperature melts, sillimanite an alumina-silicate is used as a refractory, and silica is used as a binder. Depending on the fineness of the finish desired additional coatings of sillimanite and ethyl silicate may be applied. The mold thus produced can be used directly for light castings, or be reinforced by placing it in a larger container and reinforcing it more slurry.
- Just before the pour, the mold is pre-heated to about 1000 ºC (1832 ºF) to remove any residues of wax, harden the binder. The pour in the pre-heated mold also ensures that the mold will fill completely. Pouring can be done using gravity, pressure or vacuum conditions. Attention must be paid to mold permeability when using pressure, to allow the air to escape as the pour is done.
- Investment casting is better suited to castings under 100 lbs (45 kg) in weight. Because of its relatively high tooling costs and higher than average total costs, the process is normally reserved for relatively large production runs of precision products, and is not often applied to copper alloys.
- Investment casting is capable of maintaining very high dimensional accuracy in small castings, although tolerances increase somewhat with casting size. The process is unsurpassed in its ability to reproduce intricate detail.
- The types of materials that can be cast are Aluminum alloys, Bronzes, tool steels, stainless steels, Stellite, Hastelloys, and precious metals. Parts made with investment castings often do not require any further machining, because of the close tolerances that can be achieved.
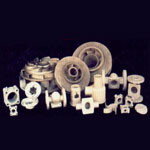
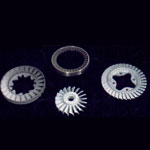
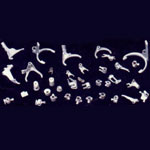
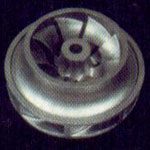
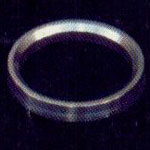
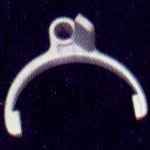