Sand Casting
INTRODUCTION
Sand casting is used to make large parts (typically Iron, but also Bronze, Brass, Aluminum). Molten metal is poured into a mold cavity formed out of sand (natural or synthetic).
In conventional sand casting, the mold is formed around a pattern by ramming sand, mixed with the proper bonding agent, onto the pattern. Then the pattern is removed, leaving a cavity in the shape of the casting to be made. If the casting is to have internal cavities or undercuts, sand cores are used to make them. Molten metal is poured into the mold, and after it has solidified the mold is broken to remove the casting. In making molds and cores, various agents can be used for bonding the sand. The agent most often used is a mixture of clay and water.
Sand casting imposes few restrictions on product shape. The only significant exceptions are the draft angles that are always needed on flat surfaces oriented perpendicular to the parting line. Dimensional control and consistency in sand castings ranges from about + 0.030 to + 0.125 in (+ 0.8 to 3.2 mm). Within this range, the more generous tolerances apply across the parting line. Surface finish ranges between approximately 300 and 500 gin (7.7 – 12.9 gm) rms.
SAND CASTING PROCESS
The pattern is housed in a box called the flask, and then packed with sand. A binder helps harden the sand into a semi-permanent shape. Once the sand mold is cured, the pattern is removed. This leaves a hollow space in the sand in the shape of the desired part. The pattern is made larger than the cast to allow for shrinkage during cooling. Sand cores can then be inserted in the mold to create holes and improve the casting`s overall shape. Simple patterns are usually open on top, allowing molten metal to be poured into them. Two-piece molds are clamped together. Molten metal is poured into a pouring cup where it will then travel down a sprue and into the gating system. Vent holes are created to allow hot gases to escape during the pour. Ideally, the pouring temperature of the molten metal is a few hundred degrees higher than the melting point, assuring good fluidity. The temperature difference also prevents premature cooling and resulting voids and porosity. After the metal cools, the sand mold is removed and the metal part is ready for additional operations, such as cutoff and grinding.
DESIGN CONSIDERATIONS
Properly locating the parting line reduces the number of cores and the amount of waste while increasing dimensional accuracy. Uniform casting thickness results in uniform cooling and solidification, as well as distortion-free castings. When uniform cross sections cannot be maintained, gradual changes in cross sections are required. This can be achieved by using a transition radius of 1/3 of the thicker section and blending in the radius with a 15-degree slope line. To minimize problems at intersecting points within the core, use staggered rather than continuous ribs and avoid large, unsupported areas. Maintaining minimum wall thickness will prevent voids and non-fill areas. With a solid understanding of the process and its advantages, you can confidently select sand casting as the low-cost method for creating your metal components.
PRECISION DRY CASTING
The mould is dried at a temperature just above 100°C (212°F) the majority of the free moisture will be removed. This is the principal of the dry sand moulding process. Removal of the free moisture is accompanied by a significant increase in the strength and rigidity of the mould. This enables the mould to withstand much greater pressures and so, traditionally, the dry sand process has been used in the manufacture of large, heavy castings.
GREEN SAND CASTING
The relative abundance of sand and clay minerals means that the material costs for the process are low. The mould material is reclaimable, with between 90 and 95% of the sand being recycled, although new sand and additions are required to make up for the deliberately discarded loss. From an environmental view the process is also acceptable, although problems may arise from the use of organic additions to the sand and from the generation of fine silica dust. These features, combined with the relative ease of mould production, have ensured that the green sand moulding process has remained as the principal method by which castings are produced.
The green sand process remains unchallenged as the process capable of the mass production of castings at low cost, especially in cast irons.
The sand used for green sand moulding must fulfil a number of requirements:
1. It must pack tightly around the pattern, which means that it must have flowability.
2. It should be capable of being deformed slightly without cracking, so that the pattern can be withdrawn. In other words, it must exhibit plastic deformation.
3. It must have sufficient strength to strip from the patter and support its own weight without deforming, and to withstand the pressure of molten metal when the mould is cast. It must therefore have green strength.
4. It must be permeable, so that gases and steam can escape from the mould during casting.
5. It must have dry strength, to prevent erosion of the mould surface by liquid metal during pouring as the surface of the mould cavity dries out.
6. It must have refractoriness, to withstand the high temperature involved in pouring without melting or fusing to the casting.
7. With the exception of refractoriness, all of these requirements are dependent on the amount of active clay present and on the water content of the mixture
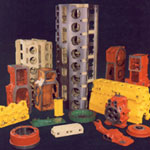
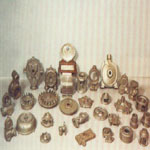
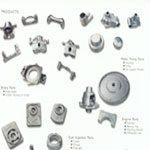