Sheet Metal Parts
Metal component parts can be stamped for lowest cost and greater efficiency.
Very intricate and complex products can be produced using a metal stamping die. This is due to advances in die design and build technologies. Products can be cut, formed, drawn, twisted, coined, extruded, welded, and tapped. Also, parts can be assembled in the die by employing a variety of technologies. As a result, the metal stamping process economically competes with other processes such as chemical etching, laser cutting, screw machining and die casting, even at low production quantities.
Very intricate and complex products can be produced using a metal stamping die. This is due to advances in die design and build technologies. Products can be cut, formed, drawn, twisted, coined, extruded, welded, and tapped. Also, parts can be assembled in the die by employing a variety of technologies. As a result, the metal stamping process economically competes with other processes such as chemical etching, laser cutting, screw machining and die casting, even at low production quantities.
It is recommended that following design parameters be kept in mind :
Avoid Sharp Corners
Internal corners should be filleted with a radius that is equal to at least one material thickness. Sharp external corners can be attained in a stamping die only by making 2 separate cuts. This most often produces a burr as the material at the intersection flows away from the cutting forces on the 2nd cut.
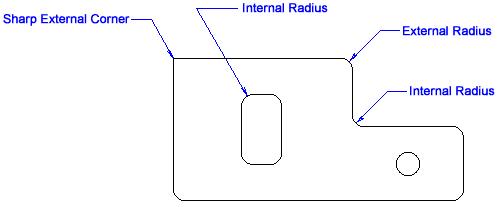
Avoid Very Small Features
Small features relative to the material thickness cause high stresses in metal stamping components. Although specialized methods exist to produce features with dimensions equal to or less than one material thickness, they decrease the capability and reliability of the metal stamping process.
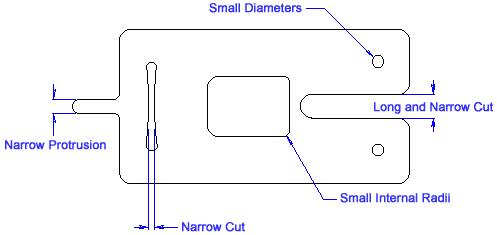
Avoid Small Bend Radii
The smallest permissible bend radius is dependent upon the material type and temper. If too small of a radius is used, the material on the outside of the bend will crack. Normally a bend radius equal to the material thickness is adequate. However, with extra hard or spring tempered copper-based material and full hard stainless steels, the bend radius should be increased to 1 1/2 to 2 times the material thickness.
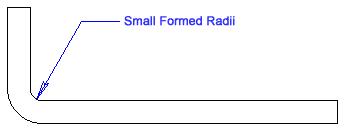
Avoid Severe Transitions on Cylindrical Parts
As a cylindrical part transitions from one diameter to another, the material must stretch. This is a result of the difference in the amount of material required for each diameter. As shown in the diagram below, this stretching must occur over a gradual transition in order to avoid tearing. It is best to utilize a transition angle no more than 45° on a medium tempered material (soft tempered material allows more, hard tempered less).
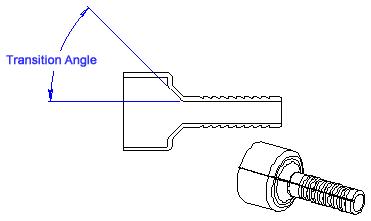
A progressive die is used to transform a flat strip of metal into a completed part. This transformation is performed incrementally, or progressively, by a series of stations that cut, form and coin the material into the desired shape.
The components that perform operations on the material are unique for every part. These components are located and guided in precision cut openings in plates which are in turn located and guided by pins. A typical die cross
The entire die is actuated by a mechanical press that moves the die up and down. The press is also responsible for feeding the material through the die, progressing it from one station to the next with each stroke.
Secondary Options
- Drilling is done in sheet metal only when piercing cannot deliver the accuracy required. For example, on a formed part, when holes on different features need to be coaxial, the accuracy obtained by machining may be required.
- Piercing is the operation of cutting internal features (holes or slots) in stock. Piercing can also be combined with other operations such as lance and form (to make a small feature such as tab), pierce and extrude (to make an extruded hole). All these operations can be combined with blanking.
- Piercing of all the holes is best done together to ensure good hole-to-hole tolerance and part repeatability. However, when there are large numbers of holes, in a tight pitch, there could be distortions. This is due to the high amount of tension on the upper surface due to stretching and compression on the bottom surface. This causes the material not to lay flat. This can be avoided/lessened by staggering the piercing of the holes. Holes are punched in a staggered pattern; then the other holes are punched in the alternate staggered pattern.
- Tapping can be done using cut threads or formed threads. Formed threads (thread rolling) is preferable as fewer burrs are generated.
- Welding is the process of permanently joining two or more metal parts, by melting both materials. The molten materials quickly cool, and the two metals are permanently bonded. Spot welding and seam welding are two very popular methods used for sheet metal parts.
- Spot welding is primarily used for joining parts that normally upto 3 mm (0.125 in) thickness.
- Spot-weld diameters range from 3 mm to 12.5 mm (0.125 to 0.5 in) in diameter.
- Low carbon steel is most suitable for spot welding. Higher carbon content or alloy steels tend to form hard welds that are brittle and could crack. This tendency can be reduced by tempering.
- Austenitic Stainless steels in the 300 series can be spot welded as also the Ferritic stainless steels. Martensitic stainless steels are not suitable since they are very hard.
- Aluminums can be welded using high power and very clean oxide free surfaces. Cleaning the surface to be oxide-free, adds extra costs (that can be avoided with low carbon steel).
- Dissimilar materials cannot be spot welded due to different melt properties and thermal conductivities. Plated steel welding takes on the characteristics of the coating. Nickel and chrome plated steels are relatively easy to spot weld, whereas aluminum, tin and zinc need special preparation inherent to the coating metals.
Heat Treat
- A heat treat process is used on products that require additional strength after metal stamping. This process is used only when the formability of the final product does not allow it to be formed or coined without cracking. Therefore, the part is stamped in the soft state and then hardened.
- Although the heat treat process may be required to achieve critical performance properties, it is avoided whenever possible. Not only does it add additional cost and lead-time to products, it induces additional variation into the final part. A feature formed in the soft state will relax during heat treat. The amount of relaxation varies from part-to-part and from material lot-to-material lot, resulting in increased part variability.
Deburring
- Although most minimal burr requirements directly out of the metal stamping die, deburring is available for parts that must be free of sharp corners. Abrasive and chemical deburring options exist for all types of products.
FINISHING PLATING OPTIONS
Passivation
- Primarily used for cleaning and descaling stainless steel parts. While cleaning provides an enhanced appearance to the metal, it also ensures maximum corrosion resistance and prevents product contamination.
Electro-polishing
- Widely used to provide parts a shiny and smooth surface, e-polishing removes a few layers of atoms from a part (typically .0002"-.0005"), smoothing the surfaces and rounding the edges. Often used on metal parts such as stainless steel screens and decorative items.
Tumbling
- Tumbling is used to give parts a smoother surface area, to clean, and to break sharp edges. Parts are mixed in a vibratory tumbler with a selected media.
Tin plating
- Electro-tin plating is used for excellent solderability and corrosion resistance. More details can be found at "Shielding Design Options".
Gold
- Gold plating is used in electronic parts where electrical conductivity and high corrosion resistance are required. Under Mil-G-45204 are Types I and II, grades B & C are known as hard gold . Type III, grade A is known as soft gold (best used for wire bonding). If all you need is a gold flash, only 3 to 5 millionths of an inch of Type I, grade B is needed. Specify thickness from 10u" up to 100u".
Silver
- Silver plating such as matte finish silver (Type I) and bright finish silver (Type III) are sometimes used where high electrical conductivity and excellent solderability (but decreases with age) are required. Has good corrosion resistance, depending on base metal. QQ-S-365. Specify thicknesses from <100u" up to 1000u".
Nickel
- Nickel plating is generally used to improve corrosion and wear resistance of the underlying base metal. Electroless Nickel ( Mil-C-26074) is good on flat or gently formed parts. Electroplated Nickel (QQ-N-290) is also available. Both types of nickel plating are not recommended on parts with sharp, formed features as the brittle plating will crack when the part is formed. Appearance of nickel can be similar to stainless steel in color, or an almost white, dull-grey color. Nickel plating is magnetic. Specify thicknesses ranging from 100u" up to 600u" and up.
Anodizing
- Anodizing, an electrolytic process, converts aluminum surfaces to aluminum oxide. A hard coating, and resistant to corrosion. The process changes the molecular structure of the metal surface, giving it a thin, protective film. Anodized finishes are usually colorless, but can be dyed in a variety of colors. Aluminum is often anodized, as is titanium, magnesium and tantalum.
Blackening (Black Oxide)
- For ferrous metals, a black, uniform coating commonly used for decorative purposes. Can provide very limited corrosion protection. Used to reduce light reflection, the more popular types of blackening are b lack oxide on copper and brass (Mil-F-495) and black zinc on steel (QQZ-325).