Tincoating and Differential Tincoating Line Markings
Coating Weight Tinplate
|
New Coating Designation & Nominal Coating Weight (g/m2) |
Minimum average Coating Weight (g/m2) |
Former Coating Designation |
Equally Coated |
2.8 / 2.8 |
2.45 / 2.45 |
# 25 |
5.6 / 5.6 |
5.05 / 5.05 |
# 50 |
|
8.4 / 8.4 |
7.55 / 7.55 |
# 75 |
|
11.2 / 11.2 |
10.1 / 10.1 |
# 100 |
|
Differentially Coated |
2.8 / 5.6 |
2.45 / 5.05 |
# 25 / 50 |
2.8 / 8.4 |
2.45 / 7.55 |
# 25 / 75 |
|
2.8 / 11.2 |
2.45 / 10.1 |
# 25 / 100 |
|
5.6 / 8.4 |
5.05 / 7.55 |
# 50 / 75 |
|
5.6 / 11.2 |
5.05 / 10.1 |
# 50 / 100 |
|
8.4 / 11.2 |
7.55 / 10.1 |
# 75 / 100 |
- The tin coating weight is determined in accordance with specific end use applications. Tinplate with a heavy coating weight is used for making cans that require a high corrosion resistance or
- those used bare. Tinplate with a light coating weight is used for making cans that do not require so high a corrosion resistance or those used after painting or printing.
Differential Markings
- A white line (differential marking) is painted along the edge of a differentially coated product in order to clearly indicate that it is differentially coated, and "D" is added after the coating designation symbol for the marked side (e.g., 2.8D/5.6).
- With regard to other types of differential markings.
Differentially coated tinplate
- Differentially coated tinplate, often called ‘differential tinplate’, is electrolytic tinplate, one surface of which carries a heavier coating than the other. This material is used principally for the manufacture of containers which require higher corrosion resistance inside than outside, but may occasionally be used “inside out”, for example, in packaging inert materials for shipment to tropical regions, or any other application to optimise the cost of the products.
- In order to distinguish material having differential coatings it is customary to mark one surface. Normally the heavier coated surface is marked, since this usually forms the interior of the can, but the purchaser can arrange with the supplier for the lighter surface to be marked if required.
- Various systems of marking have been used but the most common is to produce on the tinplate a series of parallel lines about 1 mm wide. This is accomplished by roller “printing”, using a dichromate solution, on the tinplate surface prior to flow-melting. After melting the marking appears as a slightly dull line pattern against a bright background.
- The normal way is to issue a simple line (75mm spaced) marking to indicate that the material is differential, and not equally coated tinplate. Some users prefer to identify the tin coating masses by a coded pattern of lines, but this system is now quite obsolete due to the occurrence of new coating standards.
- When marking is on the lighter coated surface, at least the alternate lines should be interrupted; on the heavier face continuous lines are used.
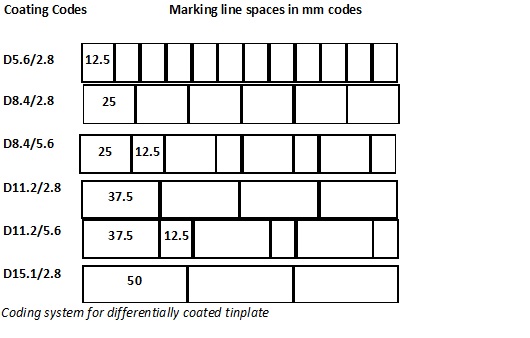
It is extremely important for the purchaser to stipulate clearly to the manufacturer both the surface to be marked and the surface which is to be piled uppermost (for sheets) or to be the exterior surface in material shipped in coil form. It is why the new European system identifies the marked face by the position of the differential letter in the coating description: D5.6/2.8 is : marking of the face coated with “5.6 g/m²” 5.6/2.8D is : marking of the face coated with “2.8 g/m²”
- Source: The International Tin Association (formerly ITRI Ltd)